personnel better. They also give you an up-to-date
account of task progression, tool and equipment
conditions, and the amount of supplies used.
PERSONNEL. When you assess your
workers performance, you will look at three
areas:
1. Attitude
2. Knowledge
3. Work habits
When making your rounds in work spaces,
assess the knowledge of the personnel working in
each space. Observe the attitude and work habits
of your people, how they handle their equipment,
and the order in which they complete jobs. Ask
subordinates questions about the job they are
doing. Knowing your peoples experience in each
area will allow you to make decisions more
quickly to achieve task accomplishment in case
of personnel setbacks.
To keep abreast of the knowledge and experi-
ence of your personnel, randomly review each
members training records. Ensure records are all
current and ensure each subordinate member is
afforded the proper path toward advancement.
MATERIAL. Make a daily inventory of
each work space to determine the amount of
materials being used so that you will know when
to draw more supplies. Also make a weekly
inventory so that you will know when to order
additional supplies for your division.
Division Supply Inventory. Each division or
department uses the operating target (OPTAR)
log to make a formal supply inventory. The
OPTAR log shows all supplies in your division.
Log all division orders in your division or
department OPTAR log. Also log (1) when an
item was ordered, (2) its stock number, (3) the
cost, (4) and the OPTAR balance. At the end of
each work week, or on whatever day you
designate, prepare an inventory sheet of all
materials and supplies in your division. This
inventory sheet will give you a running account
of all supplies.
Division Tool Inventory. Maintain your tool
inventory in much the same fashion as your supply
inventory with the following exceptions:
1. Maintain a daily power tool log. List the
name of the tool that is out of commission and
the nomenclature, stock number, and price of the
broken part. Also include a check-out and check-
in list of power tools in the log.
2. Maintain a daily hand tool log. List the
name of the tool that is out of commission and
the nomenclature, stock number, and price of the
broken part. Include a check-out and check-in list
of hand tools in the hand tool log.
3. Ensure all hand and power tools are
assigned serial numbers; enter serial numbers into
each log for easier tracking of tools.
Division Damage Control Space Inventory or
Inspection. Every division or work center should
already have a log on hand that describes
deficiencies and missing equipment in each of
your spaces. That log is called the equipment
deficiency log (EDL). The EDL contains informa-
tion such as (1) the space, (2) space location, (3)
the problem or deficiency, (4) when it was
discovered, and (5) action taken. For missing
equipment the EDL will contain information on
(1) nomenclature of missing equipment, (2) stock
number, (3) when it was placed on order, and (4)
the form or forms used to order the missing
equipment.
Work Center Requirements and
Personnel Deficiencies
For a work center to accomplish its goals and
maintain an effective degree of operational
readiness, it must maintain its most valuable
resourceits personnel.
Just as you have a supply inventory for your
division, the command maintains an inventory of
people available. That inventory is called the
enlisted distribution verification report (EDVR).
From this report a division can better enable itself
to fulfill any TAD requirements without an
adverse effect on its work force.
MANNING REQUIREMENTS. The
EDVR is a computer printout of the number of
personnel in each rate aboard the command. The
EDVR lists personnel by order of rank and the
amount of each rate allowable aboard the
command.
TAD REQUIREMENTS. Commands have
a set amount of personnel it can provide for
various TAD requirements and different schools.
The TAD requirements are usually divided
throughout the various departments based on the
ships overall manpower.
2-2
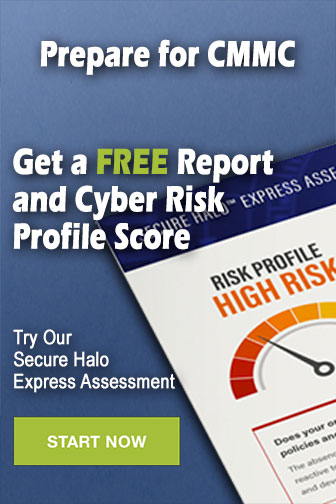