Figure 3-4.-Sample Gantt chart.
review technique (PERT) while constructing the
Polaris fleet ballistic missile. It focuses on key
points and steps that may present potential
problems. You will find PERT helpful when
scheduling complicated nonrepetitive tasks and as
a device to evaluate and report progress.
The PERT uses a line chart to show the
relationship of tasks and the time required to
complete each task. The chart contains lines and
nodes (circles) that represent the start and
completion of tasks.
When using the PERT, you apply a mathe-
matical formula instead of guesswork to figure
the time needed to perform a task. You need three
time estimates to complete the formula. First,
estimate an optimistic time (TO) based on a
minimum of difficulties that could occur. Second,
estimate a pessimistic time (Tp) based on the
maximum difficulties that could occur. Third,
estimate a normal completion time (Tn) based on
the average time you could expect to complete the
task. The formula for figuring estimated PERT
time (Te) is as follows:
To construct a PERT network, follow the six
basic steps applied to all PERT projects. First,
identify the component task you will perform.
Second, define the order in which you need to
complete the component task. Third, analyze and
estimate the time required to complete each
component task and for the entire project.
Fourth, find the critical path. The critical path
is the longest path from the beginning component
task to the ending component task. Fifth, look
for ways to improve the project though modifica-
tions. Sixth, control the project. See figure 3-5
for a sample PERT chart.
Critical Path Method. The critical path
method (CPM) is very similar to the PERT. The
major difference is the PERT focuses on time
without regard to cost. The CPM focuses on both
time and cost. The CPM and PERT have three
major differences. First, the CPM only requires
a one-time estimate. Second, the CPM includes
a cost estimate as well as normal and crisis time
estimates. Third, the CPM is based on the
assumption that you have at least some experience
with the work needed to complete each component
task.
Elements of Effective Control
Control systems such as quality control or
inventory control need certain elements to be
effective: controlled work activities, timeliness,
effectiveness, accuracy, and acceptance. These
elements of control influence how the work will
be accomplished and how long work will take.
3-9
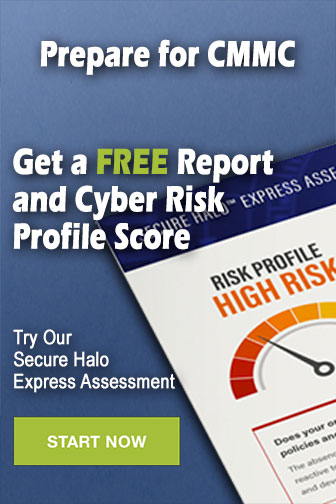