the condition of the tools in your care. PMS cards,
maintenance manuals, and technical orders often
describe the proper tool for a specific task. Safety
periodicals and other Navy publications, such as
Deckplate and Maintenance Crossfeed, provide timely
information concerning new developments in safety.
An excellent source of information concerning proper
tool use is Use and Care of Hand Tools and Measuring
Tools, NAVEDTRA 14256.
PROGRESS CHECKS
As mentioned earlier, you begin a job by
developing a plan and organizing the steps and the
resources needed. Without a definite job plan and
organized steps, you will have no way to judge the
progress of the job. Answer these five basic questions
before you begin:
1. What must be done?
2. Where should it be done?
3. When should it be done?
4. How should it be done?
5. Who should do it?
Having decided on these basic considerations, you
can begin the job. But wait; how are you going to know
whether you are doing a good job or not? Are you going
to finish on schedule? Will the finished product meet
set standards? Standards are the key to answering these
questions. To keep track of your crews progress, you
must measure the progress against some standard.
What is a standard? A standard is a basis by which
you can compare your performance against the
performance level expected by your chain of
command. Standards can consist of specifications for
tasks or equipment or a time span allowed for
completion of a test or action. For example, the
semiannual Physical Readiness Test (PRT) measures
your physical abilities in strength and endurance
against an established standard for your age group and
gender.
As a petty officer you will sometimes function as a
first-line supervisor. In that capacity you must be aware
of the performance standards that apply to your assigned
tasks. Usually either your supervisors or the technical
manuals or PMS cards that apply to the particular job set
the performance standards. Occasionally you will have
to set your own standards for performance. That may
sound difficult; but, actually, we all set standards
everyday. For example, if you decide your car is clean
enough, then you have set a personal standard for the
appearance of your vehicle. When you tell your workers
a field day is good enough, you set a standard they will
apply to other jobs. Keep that in mind when you set
standards. Make certain your standards for good
enough and best possible are the same. A superior
performer does more than just meet standards. The true
professional makes every effort possible to exceed
standards.
STATUS REPORTING
As a leader you will often encounter your
immediate superiors. There are three basic reasons
why you would want or need to contact your immediate
chain of command. First, you might go to an
upper-level supervisor when you need help. Second,
you may wish to seek advice when trying to solve an
unfamiliar problem. Third, you may be called upon to
relay information to your boss. The type of information
you relay will often involve the status of work in
progress or the mission readiness of your particular
area of responsibility. When called upon to report
information to your superiors, be careful to report
accurate up-to-date information. Dont stretch the
truth to make your section look better. Often, critical
decisions have their basis on the reported readiness of
several seemingly minor areas. Remember the four
Bs when reporting to superiors:
Be on time
Be accurate
Be brief
Be gone
PERFORMANCE FEEDBACK
Performance feedback is evaluative information
about how a job is performed. The most important
performance feedback is POSITIVE FEEDBACK.
When your people do a good job, tell them. You may be
unable to recommend them for a medal or letter of
1-9
Q8.
When reporting status to a superior there are
four Bs to remember: Be on time, Be
accurate, Be brief, and Be
1.
gone
2.
courteous
3.
formal
4.
forceful
REVIEW QUESTION
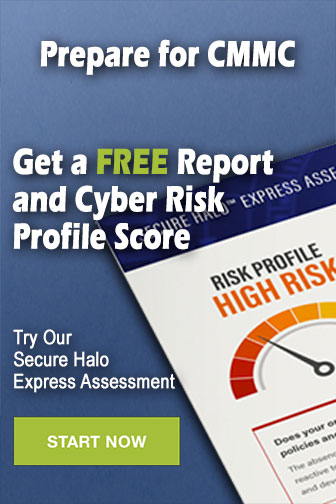