particular atmospheric contaminant, refer to
table 6-1.
NOTE: When labels only are colored, the cart-
ridge or canister will either be gray or a natural
metallic color. The National Institute for Occupa-
tional Safety and Health (NIOSH) must approve
all cartridges.
The color-coded label also specifies the max-
imum contaminant concentration level against
which the cartridge or canister provides protec-
tion. For example, a label may read as follows:
DO NOT WEAR IN ATMOSPHERES
IMMEDIATELY DANGEROUS TO
LIFE. MUST BE USED IN AREAS
CONTAINING AT LEAST 20% OXY-
GEN. DO NOT WEAR IN ATMO-
SPHERES CONTAINING MORE THAN
1/10% ORGANIC VAPORS BY VOL-
UME. REFER TO COMPLETE LABEL
ON RESPIRATOR OR CARTRIDGE
CONTAINER FOR ASSEMBLY, MAIN-
TENANCE, AND USE.
NOTE: The 20% oxygen requirement
cited above does not apply to submarines,
which may operate with an atmosphere of
as low as 18.5% oxygen.
Education is vital to the overall success of a
hearing conservation program. Make sure your
personnel receive instruction in and understand
the rationale for the following elements of the
hearing conservation program:
1.
2.
Proper wearing and maintenance of
hearing-protective devices
The command program and personnel
responsibilities for off-duty practices to
help protect hearing
Encourage your personnel to use hearing-
protective devices during off-duty activities when
they are exposed to hazardous noise sources, such
as lawn mowers, chain saws, and firearms. All
personnel exposed to gunfire in a training situa-
tion or to artillery or missile firing under any cir-
cumstances must wear hearing-protective devices.
If your personnel must work in hazardous
noise areas or with equipment that produces
sound levels greater than 84 dB or peak sound
pressure levels of 140 dB, enter them in a hear-
ing testing program. Personnel should have
received a reference hearing test upon entry into
naval service. Do not assign personnel who do not
have a reference hearing test in their health record
to duty in designated hazardous noise areas until
they receive a reference hearing test. All person-
nel should receive a hearing test periodically and
before termination of naval service.
HEARING CONSERVATION
AND NOISE ABATEMENT
HEAT STRESS
Hearing loss is recognized as an occupational
hazard related to certain trades. For example,
gunfire and rocket fire produce high-intensity im-
pulse or blast noises, which can cause hearing loss.
Hearing loss can also result from the continuous
or intermittent noises of aircraft and marine
engines and industrial activities. Hearing loss has
been and continues to be a serious concern.
Therefore, the Navy has developed a hearing con-
servation program to prevent occupational noise-
related hearing loss. The program requires the
following preventive measures:
1.
2.
The survey of work environments to iden-
tify potentially hazardous noise levels and
to identify personnel at risk
The modification of environments that
contain, or equipment that produces,
potentially hazardous noise to reduce the
noise level to acceptable levels whenever
technologically and economically feasible
Heat stress is the strain placed on the body
as it attempts to regulate its temperature as a result
of any combination of air temperature, thermal
radiation, humidity, air flow, and work load. This
condition can readily produce fatigue, severe
headache, nausea, and poor physical and mental
performance. Prolonged exposure will cause heat
exhaustion or heat stroke and severe impairment
of the bodys temperature-regulating ability. If
not properly treated, these conditions can be life
threatening.
Adhere to the commands Heat Stress Pro-
gram by reporting heat stress conditions as they
occur. Educate your division about the Heat
Stress Program, the identification of heat stress
conditions, stay time, and rotation of personnel.
Heat stress has occurred in engineering spaces,
laundries, sculleries, steam catapult spaces, and
workshops aboard our ships. In many instances,
clogged ventilation systems, damaged or missing
6-12
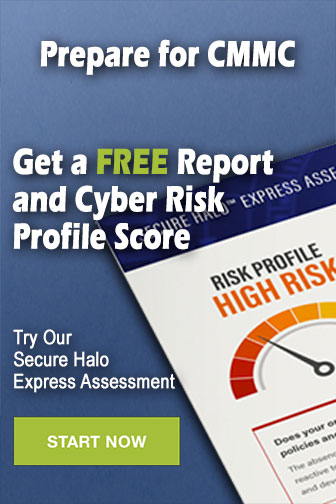