Always insisting on having full respon-
sibility for each task you are assigned
Demonstrating self-control in a conflict or
when you are provoked
Total Quality Management (TQM)
A major problem facing the armed services
today is a lack of money. The budgets of our
forces are not going to increase in the foreseeable
future. Indeed, they will probably continue to
shrink. Although our present system of doing
business is adequate, it doesnt allow for many
improvements in productivity. We have done an
excellent job with our present system. To wring
any more bang from our buck, however, will
mean a change in the way we do business.
Management by objectives is a time-honored
principle of management. However, we now must
change our objectives. Todays managers must set
their sights on a larger, system-wide objective.
That objective is increased productivity through
better quality.
The Department of the Navy (DON) has
recently adopted the concept of Total Quality
Management (TQM) as the means of meeting
DON needs into the 21st century. Executive Order
12637, signed April 27, 1988, establishes the
Productivity Improvement Program for the
federal government. TQM IS THE NAVYS
ANSWER TO THAT ORDER. The Navy has
adopted the civilian TQM concept and changed
the name to a more military sounding name
Total Quality Leadership (TQL).
TQM, What Is It?
TQM focuses on the process by which work
gets done. The person most familiar with that
process is the individual worker responsible for
making it work. Often, a process is either
unmanageable or just plain unworkable. In a rigid
bureaucracy, for workers to persuade upper
echelons of a need to change a procedure is
nearly impossible. Under TQM, management is
responsible for making a particular job as easy
as possible for workers. Supervisors and managers
monitor the work process and respond to
suggestions from the work force concerning
unworkable procedures. Sailors in particular are
infamous for coming up with nonstandard (but
workable) solutions to problems. In some cases,
this results in unsafe practices. However, these
solutions are often extremely practical. We must
develop the ability to ferret out these improve-
ments and incorporate them into standard
procedures. That serves a dual purpose. First, it
ensures the recommended improvement is usable
and meets all applicable standards. Second, the
improved method is made available to everyone
involved in that process. Both of these purposes
serve a practical application of "working smarter,
not harder."
Benefits of TQM
A popular myth among military managers
holds that increased quality results in increased
costs and decreased productivity. In reality,
improved quality ultimately results in decreased
costs and increased productivity. How can this be?
A focus on quality extends the time between
failures on equipment and improves the efficiency
of our operations. It reduces rework requirements
as well as the need for special waivers of
standards. It also reduces mistakes and produces
monetary savings through more efficient use of
scarce resources.
Direct benefits of TQM are as follows:
Increased pride of workmanship among
individual workers
Increased readiness
Improved sustainability caused by extended
time between equipment failures
Greater mission survivability
Better justification for budgets because of
more efficient operations
Streamlined maintenance and production
processes
The bottom line of TQM is more bang for
the buck.
The Concept of Quality Management
The concept behind quality management
revolves around a change from management by
results to management by process (quality)
improvement. Managers are tasked with con-
tinuously improving each and every process
in their organization. That means combining
quantitative methods and human resource manage-
ment techniques to improve customer-supplier
3-21
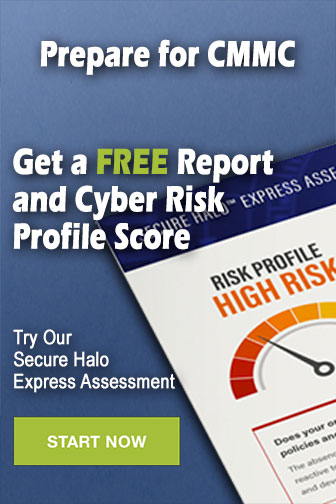